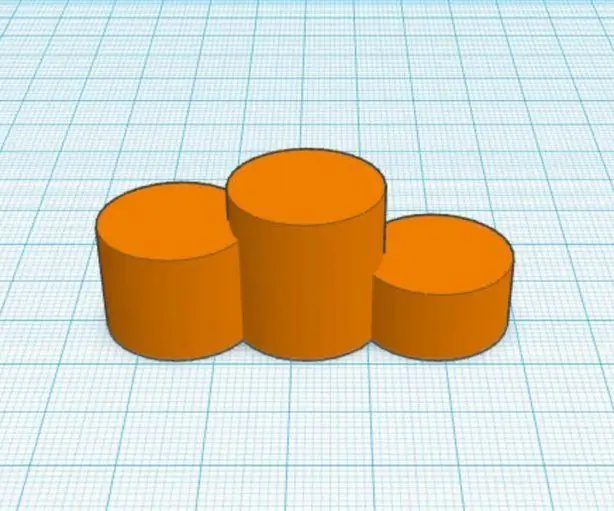
İçindekiler:
- Adım 1: Likit Kristal Ekranların Temelleri
- Adım 2: GreenPAK Tasarım Temel Blok Şeması
- Adım 3: Mevcut Tüketimi Tasarlayın
- Adım 4: GreenPAK Cihaz Şeması
- Adım 5: I²C Arayüzü
- Adım 6: Çıkış Segmenti Sürücüsü
- Adım 7: Dahili Osilatör ve Arka Panel Saat Kaynak Kontrolü
- Adım 8: Arka Panel Saat Çıkışı veya Segment 15 Çıkış Pin Kontrolü
- Adım 9: LCD Sistem Prototipi
- Adım 10: LCD Kontrolü için I²C Komutları
- Adım 11: LCD Testi için I²C Komutları
- Adım 12: Test Sonuçları
2025 Yazar: John Day | [email protected]. Son düzenleme: 2025-06-01 06:10
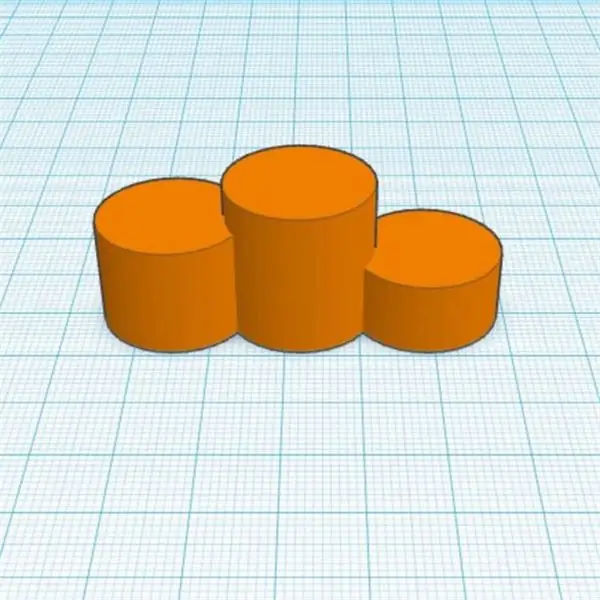
Likit Kristal Ekranlar (LCD), iyi görsel özellikleri, düşük maliyeti ve düşük güç tüketimi nedeniyle ticari ve endüstriyel uygulamalarda yaygın olarak kullanılmaktadır. Bu özellikler, LCD'yi taşınabilir enstrümanlar, hesap makineleri, saatler, radyolar vb. gibi pille çalışan cihazlar için standart çözüm haline getirir.
Bununla birlikte, LCD'nin neyi gösterdiğini düzgün bir şekilde kontrol etmek için LCD'nin elektronik sürücüsü, LCD pinlerine uygun voltaj dalga biçimleri üretmelidir. DC (doğru akım) gerilimler cihaza kalıcı olarak zarar vereceğinden dalga biçimleri AC (alternatif akım) olmalıdır. Uygun sürücü, bu sinyalleri minimum güç tüketimiyle LCD'ye kaynaklayacaktır.
Bireysel segment kontrolü için yalnızca bir arka panel ve bir pim içeren Statik ve her bir pim için birden fazla arka düzlem ve birden çok segmentin bağlı olduğu Multiplexed olmak üzere iki tür LCD vardır.
Bu Eğitim Tablosu, SLG46537V GreenPAK™ cihazı ile bir statik LCD sürücünün tasarımını sunacaktır. Tasarlanan LCD sürücüsü, güç kaynağından gelen birkaç mikroamperlik akımı kullanarak 15 adede kadar LCD segmentini çalıştırır ve kontrol için bir I²C arabirimi sunar.
Aşağıdaki bölümlerde gösterilecektir:
● LCD'ler hakkında temel bilgiler;
● ayrıntılı olarak SLG46537V GreenPAK LCD sürücü tasarımı;
● iki GreenPAK cihazıyla yedi segmentli, 4 basamaklı statik LCD'nin nasıl sürüleceği.
Aşağıda, çözümün I²C arabirimli statik LCD sürücüsünü oluşturmak için nasıl programlandığını anlamak için gereken adımları açıkladık. Ancak, sadece programlamanın sonucunu almak istiyorsanız, halihazırda tamamlanmış GreenPAK Tasarım Dosyasını görüntülemek için GreenPAK yazılımını indirin. GreenPAK Geliştirme Kitini bilgisayarınıza takın ve I²C arayüzlü statik LCD sürücüsünü oluşturmak için programa basın.
Adım 1: Likit Kristal Ekranların Temelleri
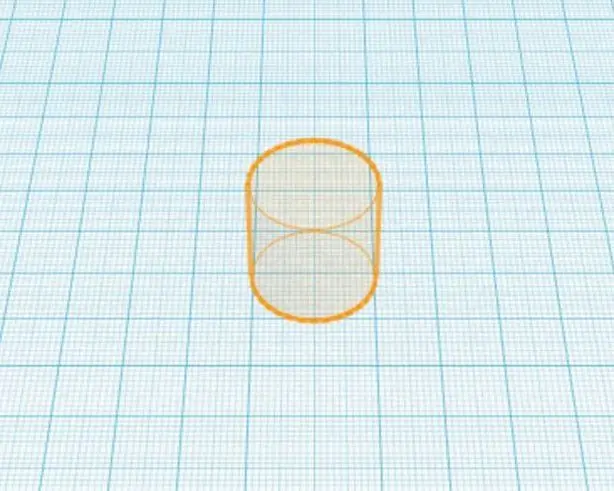
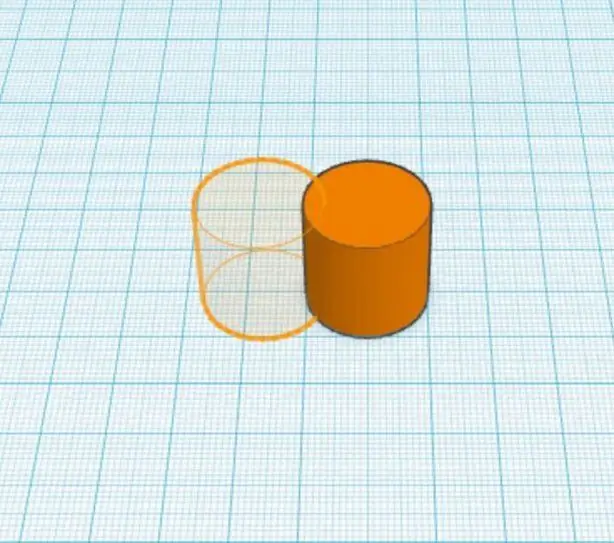
Sıvı Kristal Ekranlar (LCD) ışık yaymayan bir teknolojidir, yalnızca harici bir ışık kaynağının nasıl geçtiğini kontrol eder. Bu harici ışık kaynağı, yansıtıcı ekran tipinde mevcut ortam ışığı veya aktarıcı ekran tipinde bir arka ışık ledinden veya lambadan gelen ışık olabilir. LCD'ler iki cam plaka (üst ve alt), aralarında ince bir sıvı kristal (LC) tabakası ve iki ışık polarizörü (Uygulama Notu AN-001 - LCD Teknolojisinin Temelleri, Hitachi, Uygulama Notu AN-005 - Ekran) ile yapılmıştır. Modlar, Hitachi). Polarizör, hafif elektromanyetik alan için bir ışık filtresidir. Diğer bileşenler bloke olurken, sadece doğru elektromanyetik alan yönündeki ışık bileşenleri polarizörden geçer.
Sıvı kristal, ışığın elektromanyetik alanını 90 derece veya daha fazla döndüren organik bir malzemedir. Ancak, LC'ye bir elektrik alanı uygulandığında ışığı artık döndürmez. Üst ve alt ekran camına şeffaf elektrotların eklenmesiyle, ışığın ne zaman geçip geçmediğini harici bir elektrik alanı kaynağı ile kontrol etmek mümkündür. Yukarıdaki Şekil 1 (bkz. Uygulama Notu AN-001 - LCD Teknolojisinin Temelleri, Hitachi) bu işlem kontrolünü göstermektedir. Şekil 1'de, elektrik alanı olmadığında ekran karanlıktır. Bunun nedeni, her iki polarizörün de ışığı aynı yönde filtrelemesidir. Polarizörler ortogonal ise, elektrik alanı mevcut olduğunda ekran karanlık olacaktır. Bu, yansıtıcı ekranlar için en yaygın durumdur.
LCD'yi kontrol etmek için minimum elektrik alanı veya voltajı AÇIK eşiği olarak adlandırılır. LC sadece voltajdan etkilenir ve LC malzemesinde hemen hemen hiç akım yoktur. LCD'deki elektrotlar küçük bir kapasitans oluşturur ve bu bir sürücü için tek yüktür. LCD'nin görsel bilgileri göstermek için düşük güçlü bir cihaz olmasının nedeni budur.
Ancak, LCD'nin bir doğru akım (DC) voltaj kaynağı ile çok uzun süre çalışamayacağını unutmamak önemlidir. DC voltajının uygulanması, LC malzemesinde kimyasal reaksiyonlara neden olarak, malzemeye kalıcı olarak zarar verecektir (Uygulama Notu AN-001 - LCD Teknolojisinin Temelleri, Hitachi). Çözüm, LCD elektrotlarına alternatif bir voltaj (AC) uygulamaktır.
Statik LCD'lerde, bir cama bir arka panel elektrotu yerleştirilmiştir ve ayrı LCD segmentleri veya pikselleri diğer cama yerleştirilmiştir. Bu, en basit LCD türlerinden biridir ve en iyi kontrast oranına sahip olanıdır. Ancak, bu tür bir ekran genellikle her bir segmenti kontrol etmek için çok fazla pin gerektirir.
Genel olarak, bir sürücü kontrolörü, arka düzlem için bir kare dalga saat sinyalini ve ön düzlemdeki bölümler için bir saat sinyalini birlikte sağlar. Arka panel saati, segment saati ile aynı fazda olduğunda, her iki düzlem arasındaki ortalama karekök (RMS) voltajı sıfırdır ve segment şeffaftır. Aksi takdirde, RMS voltajı LCD AÇIK eşiğinden yüksekse segment kararır. Arka düzlem, açık ve kapalı segment için dalga biçimleri Şekil 2'de gösterilmektedir. Şekilde görülebileceği gibi, ON segmenti arka plan sinyaline göre faz dışıdır. Kapalı segment, arka plan sinyaline göre aynı fazdadır. Düşük maliyetli, düşük güçlü ekranlar için uygulanan voltaj 3 ile 5 volt arasında olabilir.
LCD'nin arka paneli ve bölümleri için saat sinyali genellikle 30 ila 100 Hz aralığındadır, bu, LCD'de görsel bir titreme etkisinden kaçınmak için minimum frekanstır. Genel sistemin güç tüketimini azaltmak için daha yüksek frekanslardan kaçınılır. LCD ve sürücülerden oluşan sistem, mikroamper sırasına göre çok az akım tüketecektir. Bu, onları düşük güç ve pil güç kaynağı kaynağı uygulamaları için mükemmel şekilde uygun hale getirir.
Aşağıdaki bölümlerde, ticari bir LCD için arka panel saat sinyalini ve bireysel segment saat sinyalini üretebilen GreenPAK cihazı ile bir LCD statik sürücü tasarımı ayrıntılı olarak sunulmaktadır.
Adım 2: GreenPAK Tasarım Temel Blok Şeması
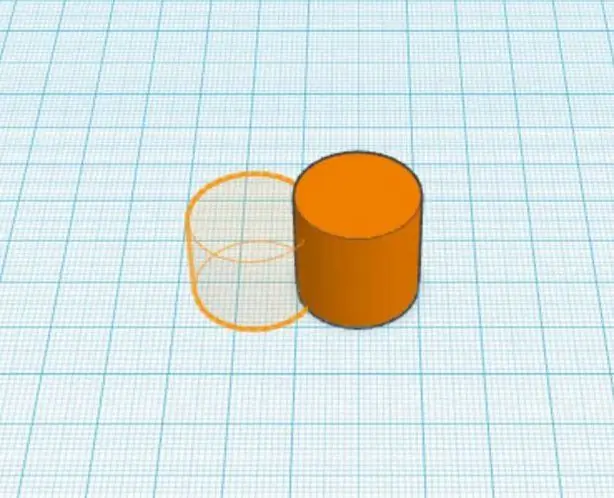
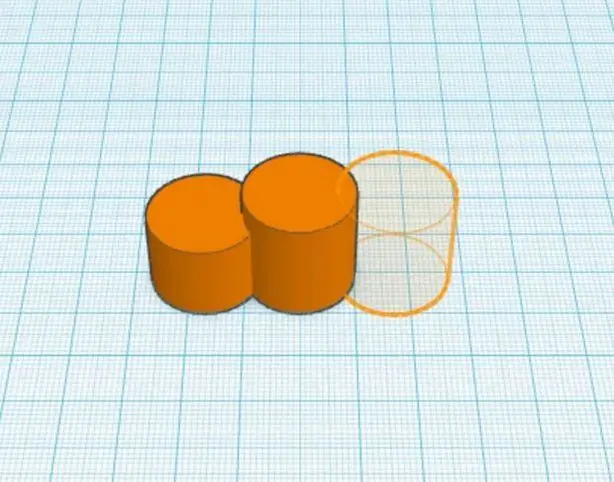
GreenPAK tasarımını gösteren bir blok diyagram Şekil 3'te gösterilmiştir. Tasarımın temel blokları I²C arayüzü, çıkış segmenti sürücüsü, dahili osilatör ve arka panel saat kaynağı seçicisidir.
I²C arayüz bloğu, her bir bireysel segment çıkışını ve LCD'nin arka panel saat kaynağını kontrol eder. I²C arayüz bloğu, segment çıkış kontrolü için tek sistem girişidir.
Dahili segment kontrol çizgisi ayarlandığında (yüksek seviye), ilgili LCD segmenti koyu opaktır. Dahili segment kontrol hattı sıfırlandığında (düşük seviye) ilgili LCD segmenti şeffaftır.
Her dahili segment kontrol hattı bir çıkış sürücüsüne bağlıdır. Çıkış segmenti sürücü bloğu, şeffaf segmentler için arka panel saatiyle ilişkisi olan bir faz içi saat sinyali üretecektir. Karanlık bölümler için, bu sinyal, arka panel saati ile ilişkisi ile faz dışıdır.
Arka panel saat kaynağı da I²C arayüzü ile seçilir. Dahili arka panel saat kaynağı seçildiğinde dahili osilatör açılır. Dahili osilatör 48 Hz'lik bir saat frekansı üretecektir. Bu sinyal, çıkış segmenti sürücü bloğu tarafından kullanılacak ve arka panel saat çıkış pinine (GreenPAK pin 20) adreslenecektir.
Harici arka panel saat kaynağı seçildiğinde dahili osilatör kapatılır. Çıkış segmenti sürücü referansı, harici arka panel saat girişidir (GreenPAK pin 2). Bu durumda, arka panel saat çıkış pimi, OUT15 segmenti olan ek bir segment kontrol hattı olarak kullanılabilir.
Aynı I²C hattında birden fazla GreenPAK cihazı kullanılabilir. Bunun için her cihazın farklı bir I²C adresi ile programlanması gerekir. Bu şekilde sürülen LCD segmentlerinin sayısını artırmak mümkündür. Bir cihaz, 14 segmenti çalıştırarak arka panel saat kaynağını oluşturmak üzere yapılandırılır ve diğerleri, harici bir arka panel saat kaynağı kullanmak üzere yapılandırılır. Her ek cihaz bu şekilde daha fazla 15 segmenti çalıştırabilir. Aynı I²C hattına 16 adede kadar cihazı bağlamak ve ardından bir LCD'nin 239 adede kadar bölümünü kontrol etmek mümkündür.
Bu Eğitilebilir Kitapta, bu fikir, 2 GreenPAK cihazıyla bir LCD'nin 29 segmentini kontrol etmek için kullanılır. Cihaz pin çıkışı işlevselliği Tablo 1'de özetlenmiştir.
Adım 3: Mevcut Tüketimi Tasarlayın
Bu tasarımdaki önemli bir endişe, mümkün olduğu kadar düşük olması gereken akım tüketimidir. GreenPAK cihazının tahmini hareketsiz akımı, 3,3 V besleme işlemi için 0,75 µA ve 5 V besleme işlemi için 1,12 µA'dır. Dahili osilatörün akım tüketimi, 3,3 V ve 5 V güç kaynağı çalışması için sırasıyla 7,6 µA ve 8,68 µA'dır. Bu tasarım düşük saat frekansında çalıştığından, anahtarlama kayıplarından akım tüketiminde önemli bir artış olması beklenmemektedir. Bu tasarım için tüketilen tahmini maksimum akım, dahili osilatör açıkken 15 µA'dan ve dahili osilatör kapalıyken 10 μA'dan düşüktür. Her iki durumda da tüketilen ölçülen akım, Test Sonuçları Bölümünde gösterilir.
Adım 4: GreenPAK Cihaz Şeması
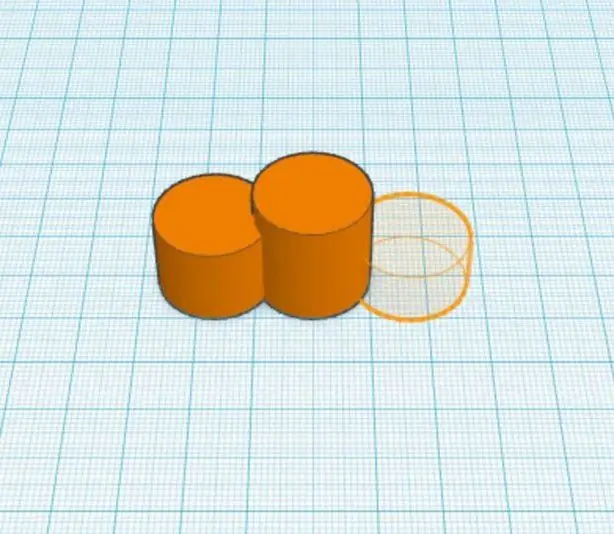
GreenPAK yazılımında tasarlanan proje Şekil 4'te gösterilmiştir. Bu şema referans olarak temel blok diyagramları kullanılarak anlatılacaktır.
Adım 5: I²C Arayüzü
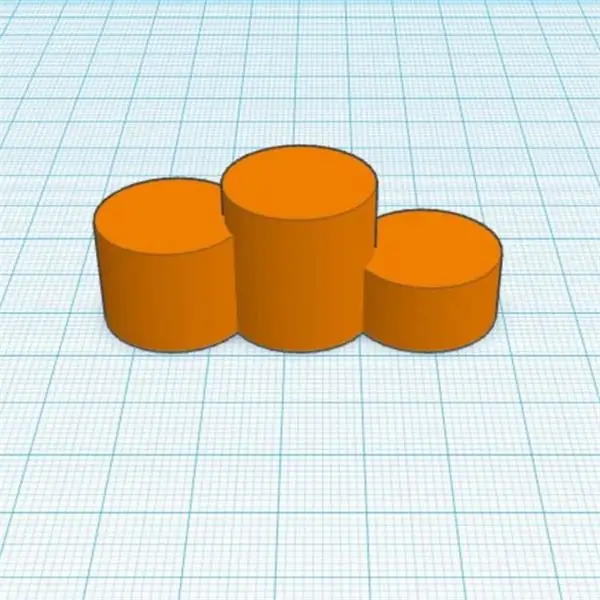
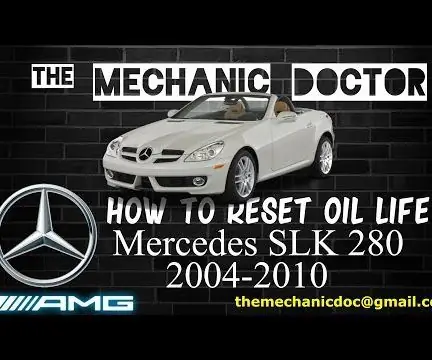
I²C arayüz bloğu, cihaz çalışma kontrolünün ana kontrol bloğu olarak kullanılır. Blok bağlantılarına ve konfigüre edilmiş özelliklere yakından bir bakış Şekil 5'te gösterilmektedir.
Bu blok, sırasıyla I²C SCL ve SDA pinleri olan PIN 8 ve PIN 9'a bağlanır. Cihazın içinde, I²C bloğu 8 Sanal Giriş sunar. Her Sanal Giriş için başlangıç değeri, özellikler penceresinde gösterilir (bkz. Şekil 5). OUT0'dan OUT6'ya kadar olan sanal girişler, segment kontrol hatları olarak kullanılır. Bu kontrol hatları, segment çıkışı 1 ila segment çıkışı 7'ye karşılık gelir ve segment çıkış sürücüsüne bağlanır. Sanal Giriş OUT7, BCKP_SOURCE net adıyla arka panel saat kaynağı seçici hat kontrolü olarak kullanılır. Bu ağ tasarımdaki diğer bloklar tarafından kullanılacaktır. I²C kontrol kodu, projedeki her IC için farklı bir değerle yapılandırılır.
Yukarıdaki Şekil 6'da gösterildiği gibi Asenkron Durum Makinesi (ASM) çıkışında 8 dahili segment kontrol hattı daha mevcuttur. Segment çıkış satırı 8 (özellikler penceresinde SEG_OUT_8), segment çıkış hattı 15 (SEG_OUT_15) aracılığıyla 0 durumunda ASM çıkışı tarafından kontrol edilir. ASM bloğunda herhangi bir durum geçişi yoktur, her zaman 0 durumundadır. ASM çıkışları segment çıkış sürücülerine bağlı.
Segment çıkış sürücüleri, cihazın çıkış sinyalini üretecektir.
Adım 6: Çıkış Segmenti Sürücüsü
Çıkış segmenti sürücüsü, temel olarak XOR mantık bağlantı noktası olarak yapılandırılmış bir Arama tablosudur (LUT). Her çıkış segmenti için, segment kontrol hattına ve arka panel saatine (BCKP_CLOCK) bağlı bir XOR portu olmalıdır. XOR portu, çıkış segmentine faz içi ve faz dışı sinyal üretmekten sorumludur. Segment kontrol hattı yüksek seviyede olduğunda, XOR port çıkışı arka panel saat sinyalini tersine çevirecek ve segment pinine faz dışı bir sinyal üretecektir. LCD arka paneli ile LCD segmenti arasındaki voltaj farkı, bu durumda LCD segmentini karanlık segment olarak ayarlayacaktır. Segment kontrol hattı düşük seviyede olduğunda, XOR port çıkışı arka panel saat sinyalini takip edecek ve ardından segment pinine faz içi bir sinyal üretecektir. Bu durumda LCD arka paneli ile segment arasına voltaj uygulanmadığından, segment ışığa karşı şeffaftır.
Adım 7: Dahili Osilatör ve Arka Panel Saat Kaynak Kontrolü
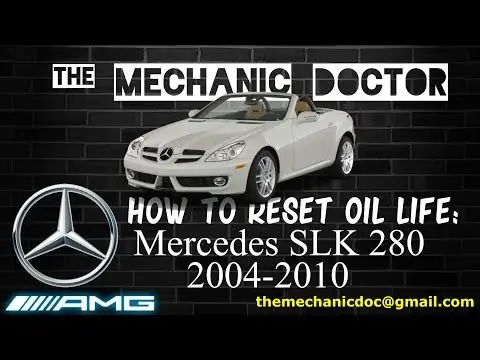
Dahili osilatör, I²C arayüzünden gelen BCKP_CLOCK sinyali yüksek bir seviyeye ayarlandığında kullanılır. Saat kaynağı kontrol şemasının yakından görünümü, yukarıdaki Şekil 7'de gösterilmektedir.
Osilatör, OUT0 (8/64) osilatöründe mevcut olan en yüksek çıkış bölücüsü ile 25 kHz RC frekansı olarak yapılandırılmıştır. Tüm konfigürasyon Şekil 7'de gösterilen özellikler penceresinde görülmektedir. Bu şekilde dahili osilatör 48 Hz'lik bir saat frekansı üretecektir.
Osilatör sadece BCKP_SOURCE sinyali POR sinyali ile birlikte yüksek seviyede olduğunda aktiftir. Bu kontrol, bu iki sinyali 4-L1 LUT'un NAND bağlantı noktasına bağlayarak yapılır. NAND'ın çıkışı daha sonra osilatör kapatma kontrol pininin girişine bağlanır.
BCKP_SOURCE sinyali, 3-L10 LUT ile oluşturulmuş MUX'u kontrol eder. BCKP_SOURCE sinyali düşük seviyede olduğunda, arka panel saat kaynağı PIN2'den gelir. Bu sinyal yüksek seviyede olduğunda, arka plan saat kaynağı dahili osilatörden gelir.
Adım 8: Arka Panel Saat Çıkışı veya Segment 15 Çıkış Pin Kontrolü
Bu tasarımdaki Pin 20, seçilen arka panel saat kaynağına bağlı olarak çift fonksiyona sahiptir. Bu pinin çalışması, Şekil 8'de gösterildiği gibi bir adet 4 girişli LUT ile kontrol edilir. 4 bitlik bir LUT ile, XOR portunun çalışmasını bir MUX çıkışı ile ilişkilendirmek mümkündür. BCKP_SOURCE sinyali yüksek seviyede olduğunda, LUT çıkışı dahili osilatör saatini takip edecektir. Ardından pin 20, arka panel saat çıkışı olarak çalışır. BCKP_SOURCE sinyali düşük seviyede olduğunda, LUT çıkışı ASM çıkışından SEG_OUT_15 ile arka plan saat sinyali arasındaki XOR işlemi olacaktır. Bu işlemi yapacak 4 bitlik LUT yapılandırması Şekil 8'de gösterilmektedir.
Adım 9: LCD Sistem Prototipi

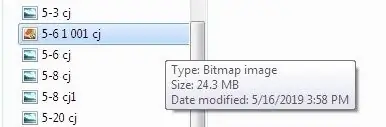
GreenPAK tasarım çözümünün kullanımını göstermek için bir devre tahtasına bir LCD sistem prototipi monte edildi. Prototip için, yedi segmentli, 4 basamaklı bir statik LCD, DIP kartındaki iki GreenPAK cihazı tarafından çalıştırılır. Bir cihaz (IC1), LCD arka panelini sürmek için dahili osilatörü kullanır ve diğer cihaz (IC2) bu sinyali arka panel giriş referansı olarak kullanır. Her iki IC, minimum geliştirme kartında bir STM32F103C8T6 mikro denetleyici (MCU) tarafından I²C arayüzü üzerinden kontrol edilir.
Şekil 9, iki GreenPAK IC, LCD ekran ve MCU kartı arasındaki bağlantıların şemasını göstermektedir. Şematikte, U1 (IC1) referanslı GreenPAK cihazı, LCD bir ve iki rakamını (LCD sol taraf) çalıştırır. U2 (IC2) referanslı GreenPAK cihazı, LCD basamak üç ve dört artı COL segmentini (LCD sağ taraf) çalıştırır. Her iki cihazın güç kaynağı, mikrodenetleyici geliştirme kartındaki regülatörden gelir. Bir multimetre ile akım ölçümü için her GreenPAK cihazının güç kaynağı ve VDD pinleri arasına iki çıkarılabilir jumper eklenir.
Monte edilmiş prototipin bir resmi Şekil 10'da gösterilmektedir.
Adım 10: LCD Kontrolü için I²C Komutları
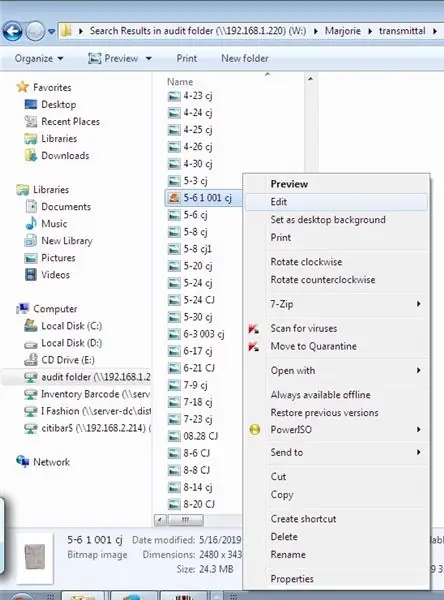

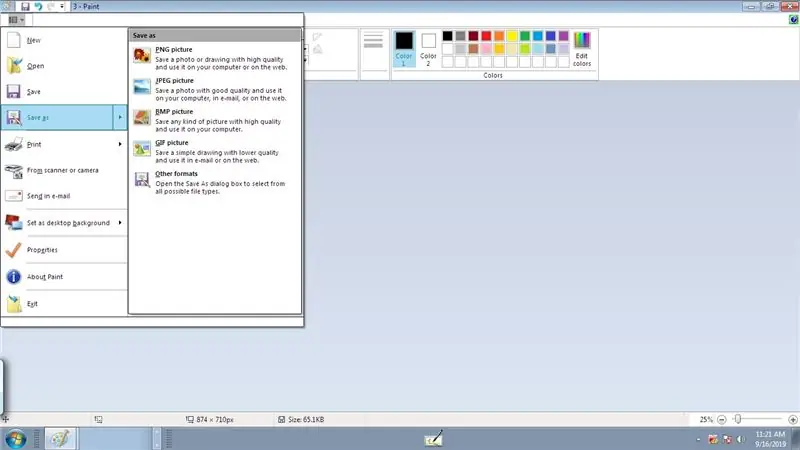
Breadboard üzerindeki iki GreenPAK cihazı, Control Byte değeri dışında aynı tasarımla programlanmıştır. IC1'in kontrol baytı 0'dır (I²C adresi 0x00), I²C kontrol baytı ise 1'dir (I²C adresi 0x10). Ekran segmentleri ve aygıt sürücüleri arasındaki bağlantılar yukarıdaki tabloda özetlenmiştir.
Daha net bir şema oluşturmak ve breadboard bağlantılarının montajını kolaylaştırmak için bağlantılar bu şekilde seçilmiştir.
Segment çıkışının kontrolü, I²C Sanal Girişlerine ve ASM çıkış kayıtlarına I²C yazma komutları ile yapılır. SLG46531V'li AN-1090 Basit I²C IO Kontrolörleri uygulama notunda açıklandığı gibi (bkz.
● Başlat;
● Kontrol baytı (R/W biti 0'dır);
● Kelime adresi;
● Veri;
● Dur.
Tüm I²C yazma komutları, Word Adresi 0xF4 (I²C Sanal Girişleri) ve 0xD0'a (durum 0 için ASM Çıkışı) yapılır. IC1'e yazma ve LCD basamak 1 ve 2'yi kontrol etme komutları Tablo 3'te özetlenmiştir. Komut dizisi gösteriminde, açık parantez “[“Başlangıç sinyalini ve yakın parantez“]” Durdurma sinyalini belirtir.
Yukarıdaki iki bayt, LCD hane 1 ve hane 2'nin kontrol segmentlerini birlikte gösterir. Burada yaklaşım, her iki bayttaki segmentleri göz önünde bulundurarak, her basamak için yazılımda ayrı bir arama tablosu (LUT) kullanmaktır. Arama tablosundaki bayt değerleri, bitsel VEYA işlemi kullanılarak karıştırılmalı ve ardından IC'ye gönderilmelidir. Tablo 4, her bir ekran basamağına yazılması gereken her sayısal değer için Bayt0 ve Bayt1 değerini göstermektedir.
Örneğin, Basamak 1'e 3 sayısını ve Basamak 2'ye 4 sayısını yazmak için, Bayt0 0xBD'dir (0x8D bit düzeyinde VEYA 0xB0 ile) ve Bayt 1 0x33'tür (0x30 bit düzeyinde VEYA 0x03 ile).
IC2'ye yazma komutu ve Basamak 3 ve 4'ü kontrol etme komutu Tablo 5'te açıklanmıştır.
3. ve 4. basamakların kontrol mantığı, 1. ve 2. basamakların kontrolü gibidir. Tablo 6, bu iki basamak için LUT'yi gösterir.
IC2'deki fark, COL segmentidir. Bu segment Byte1 tarafından kontrol edilir. Bu segmenti dark olarak ayarlamak için Byte1 ile 0x40 değeri arasında bitsel OR işlemi yapılmalıdır.
Adım 11: LCD Testi için I²C Komutları
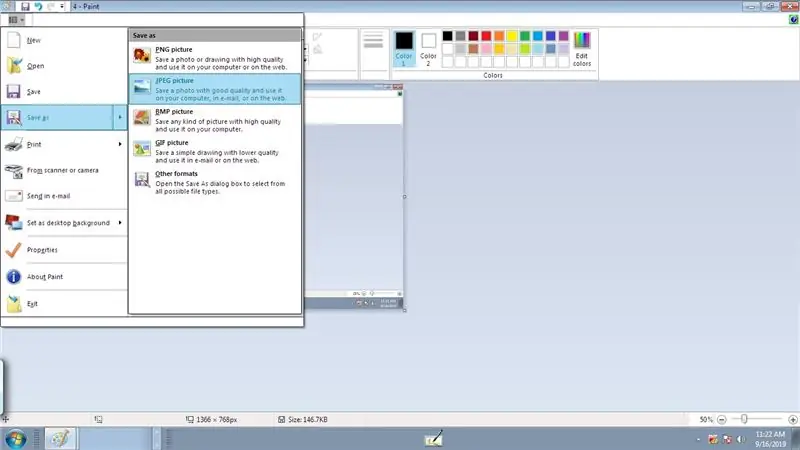
LCD testi için MCU kartı için C dilinde bir ürün yazılımı geliştirilmiştir. Bu bellenim, devre tahtasındaki her iki IC'ye bir dizi komut gönderir. Bu bellenimin kaynak kodu Ek bölümündedir. Çözümün tamamı, STM32 9.0.1 IDE için Atollic TrueStudio kullanılarak geliştirildi.
Komutların sırası ve ekranda gösterilen ilgili değerler yukarıdaki Tablo 7'de özetlenmiştir.
Adım 12: Test Sonuçları
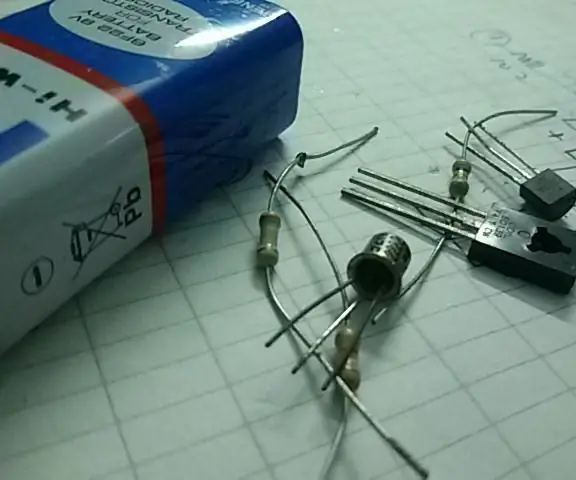
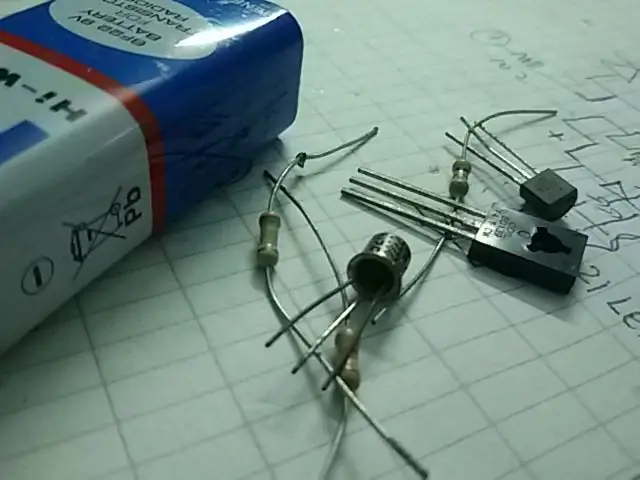
Prototip testi, bir MCU komutundan sonra ekran değerlerinin doğrulanmasından ve çalışma sırasında her bir IC tarafından akım düşüşünün ölçülmesinden oluşur.
Her bir komut değeri için LCD'nin resimleri yukarıdaki Tablo 8'de gösterilmektedir.
Her cihaz için akım düşüşü, en düşük akım aralığı olan 200 µA'da bir multimetre ile ölçülmüştür. Başlatma ve normal çalışma sırasında her cihaz için ölçülen akımın resimleri yukarıdaki Tablo 9'da gösterilmektedir.
Sonuç ve Sonuç Tartışması
GreenPAK cihazı ile düşük güçlü statik LCD sürücü tasarımı sunuldu. Bu tasarım, GreenPAK cihazlarının en büyük özelliklerinden birini açıkça göstermektedir: düşük hareketsiz akımları. GreenPAK cihazları donanım tabanlı bir çözüm olduğu için düşük frekanslı bir çalışmada, bu durumda 48 Hz'de çalışmak mümkündür. MCU tabanlı bir çözüm, periyodik olarak kısa süreler için bile daha yüksek bir çalışma frekansı gerektirecek ve daha sonra daha fazla güç çekecektir. Ve GreenPAK cihazını bir CPLD (Karmaşık Programlanabilir Mantık Cihazı) ile karşılaştırdığımızda, genellikle bir CPLD'nin 20 µA'dan daha yüksek hareketsiz bir akıma sahip olduğu açıktır.
Bu tasarımın, belirli bir projenin gereksinimlerine daha iyi uyması için kolayca değiştirilebileceğini belirtmek ilginçtir. İyi bir örnek, segment kontrolleri pin çıkışıdır. Baskılı devre kartını ve aynı zamanda yazılım geliştirmeyi basitleştirmek için kolayca değiştirilebilirler. Cihaz, kullanıma hazır bir ASIC (Uygulamaya Özel Entegre Devre) ile karşılaştırıldığında bu ilginç bir özelliktir. Genellikle, ASIC'ler geniş bir uygulama yelpazesine uyacak şekilde tasarlanmıştır ve işlemden önce IC'yi uygun şekilde yapılandırmak için bir başlangıç yazılım rutini yazılmalıdır. Güç verildikten sonra kullanıma hazır olarak başlamak üzere yapılandırılabilir bir cihaz tasarlanabilir. Bu şekilde, IC başlangıç konfigürasyonu için yazılım geliştirme süresini kısaltmak mümkündür.
Uygulamanın kaynak kodu burada Ek A'da bulunabilir.
Önerilen:
Silgi Kullanarak USB Flash Sürücü Nasıl Yapılır - DIY USB Sürücü Kutusu: 4 Adım
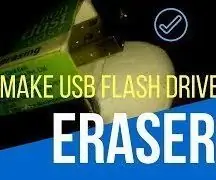
Silgi Kullanarak USB Flash Sürücü Nasıl Yapılır | Kendin Yap USB Sürücü Kutusu: Bu blog, "Silgi Kullanarak USB Flash Sürücü Nasıl Yapılır | DIY USB Sürücü Kutusu" umarım beğenirsin
Arducam ile Arduino ile CubeSat Nasıl Yapılır: 9 Adım
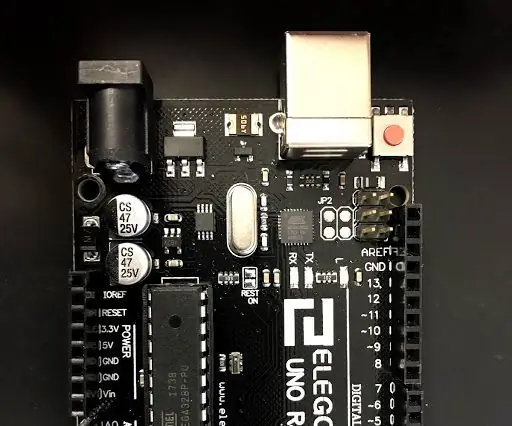
Arducam ile Arduino İle CubeSat Nasıl Yapılır: İlk resimde bir Arduino'muz var ve adı "Arduino Uno". İkinci resimde bir Arducam var ve adı "Arducam OV2640". 2MP mini."İkinci resim ile birlikte ihtiyacınız olacak malzemeler var
Alexa ile Dragonboard-410c ile Nasıl Etkileşim Yapılır: 5 Adım
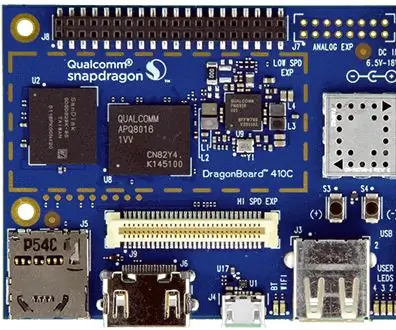
Alexa ile Dragonboard-410c ile Nasıl Etkileşim Yapılır: Bu eğitim ile Alexa'yı Dragonboard-410c'ye nasıl gömeceğinizi öğreneceksiniz. Başlamadan önce, ihtiyacınız olan bazı şeyleri tanıtalım: Alexa Voice Service (AVS) - Cihazlarınızla konuşmanızı sağlar, bulut tabanlı alexa th
Arduino UNO ile 4 Haneli Ekran Arayüzü Nasıl Yapılır: 6 Adım (Resimlerle)
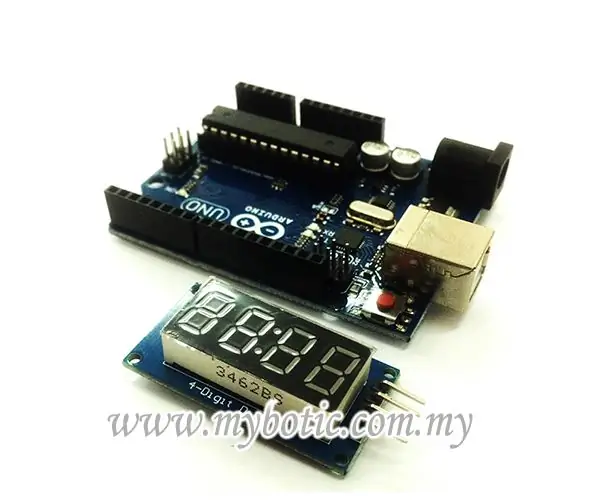
Arduino UNO ile 4 Rakamlı Ekran Arayüzü Nasıl Yapılır: Bu eğitim size Arduino UNO ile 4 Rakamlı Ekranı kullanmanın bazı temellerini öğretecek
Bir Gitar Hoparlör Kutusu Nasıl Yapılır veya Stereonuz İçin İki Adet Nasıl Yapılır: 17 Adım (Resimlerle)
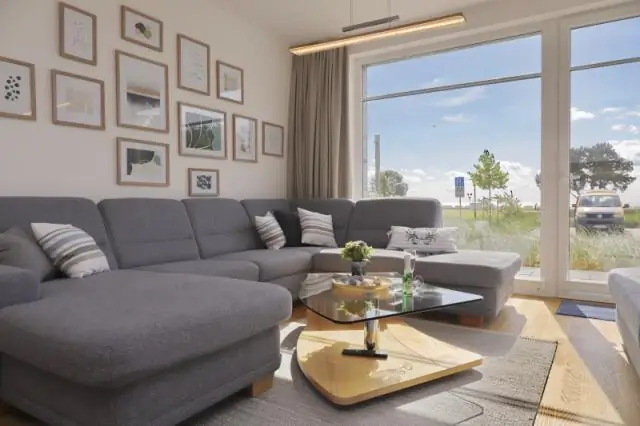
Bir Gitar Hoparlör Kutusu Nasıl Yapılır veya Stereonuz için İki Adet Yapın.: Yaptığım tüp amfi ile birlikte yeni bir gitar hoparlörü istedim. Hoparlör dükkânımda kalacak, bu yüzden çok özel bir şey olmasına gerek yok. Tolex kaplama çok kolay zarar görebilir, bu yüzden hafif bir kumdan sonra dışarıdaki siyahı püskürttüm